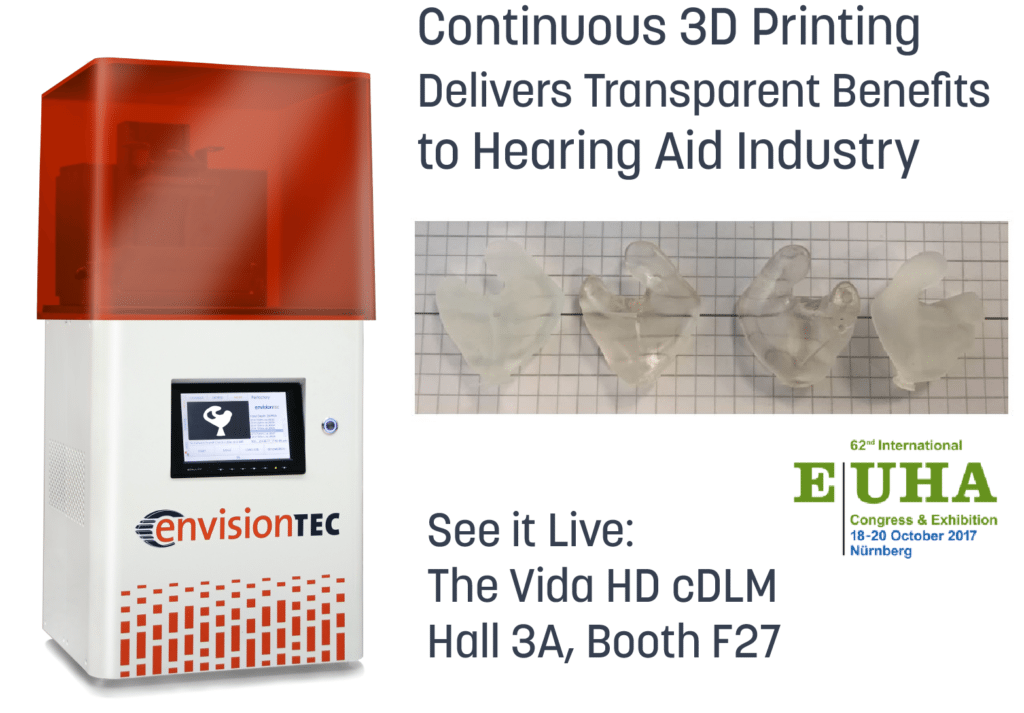
The parts in the photograph above were all printed in the same material and cleaned following the same steps with Isopropyl Alcohol. They were not polished or lacquered. The two parts in the center were printed with cDLM technology, while the parts on the outer edge were printed with DLP technology.
EnvisionTEC’s Continuous Digital Light Manufacturing (cDLM) technology offers substantial improvements over traditional Digital Light Processing (DLP) when printing hearing aid devices.
- Glass-smooth hearing aid shells and ear molds
- Transparent parts without the need for clear coating
- Unmatched Production Speed
The EnvisionTEC Vida cDLM comes in two sizes for the hearing aid sector: 90 x 50 x 100 mm and 145 x 81 x 100 mm.
Continuous technology delivers truly isotropic parts that are a step above DLP for smooth surface finish, resulting in true clarity without sanding, tumbling or coating.
Continuous technology delivers truly isotropic parts that are a step above DLP for smooth surface finish, resulting in true clarity without sanding, tumbling or coating.
In standard DLP printing, parts are built in layers or volumetric pixels (voxels) that must be peeled from the bottom tray in between exposures.
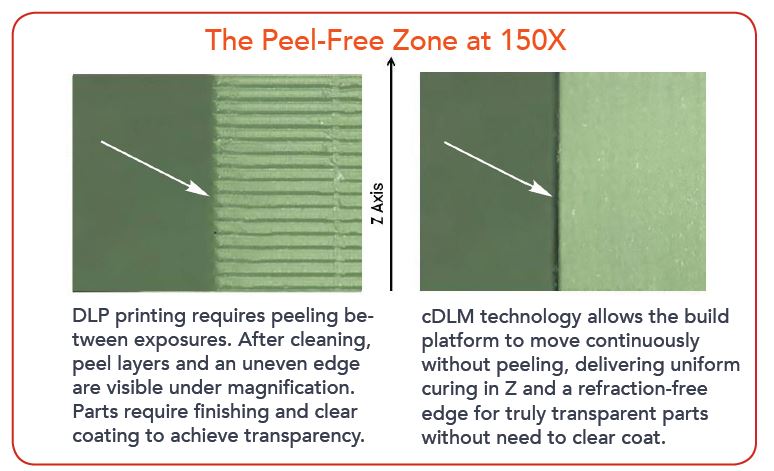