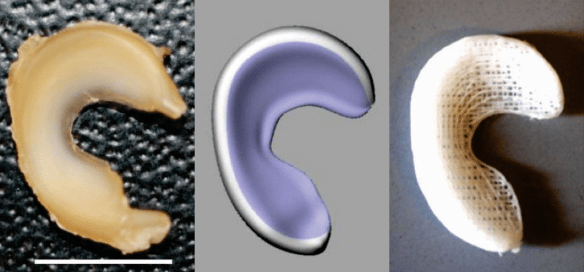
2014 was a busy year for EnvisionTEC. We kept building throughout North America with new partnerships, and won recognition at home. Take a look at some of our best moments from the year.
» Jewelry
Producing jewelry with 3D printing has never been so precise and cost effective! In March, EnvisionTEC announced the release of the Perfactory® Micro Advantage 3D printer for the high-volume jeweler. With a build envelope of 60 x 45 x 100 mm and an XY resolution as low as 50 microns, the Micro Advantage offers the same reliability and surface quality of the Micro Hi-Res with greater design capabilities. The
Perfactory® Apollo, announced in April, works with most jewelry resins and has a build envelope of 100 x 75 x 100 mm, more than two times larger than that of the Aureus.
EnvisionTEC also introduced EPIC material, featuring the casting capability of EC-500 along with the crispness of PIC needed for creating fine detail when casting or molding pieces.
» Dental
It was a big year for the dental sector in 2014 with more solutions for dental and orthodontic applications. EnvisionTEC found greater precision and clients Dental Services Group and Albensi Laboratories found widespread success. EnvisionTEC now supports more applications in digital dental and orthodontics than before, with guided surgery complemented by a new 3D printer, the Micro Drill Guide Printer, also known as the Micro DGP.

Indirect Bonding
EnvisionTEC along with Dillehay Orthodontic Lab discovered a method for performing an indirect bonding process for placing braces on patients using 3D printed models. Though 3D printed models offer greater precision and accuracy, indirect bonding is typically performed using plaster models, which allow brackets to disengage from the model onto a retainer. Most 3D printed materials adhered to the brackets, until Dillehay refined a process for using 3D printed models created with a 3SP system documented here.
In addition to this process, in 2014 EnvisionTEC developed and released a material for the creation of plastic retainers. New Ortho Tough material for both 3SP and Micro systems features the accuracy needed for creating well-fitting appliances along with the composition to support thermoforming.
Achievements in manufacturing and biomedical applications
» Manufacturing
In 2014, EnvisionTEC expanded its offerings for computer-aided manufacturing and design sectors. Whether your company is situated in consumer goods, dynamic systems, or rapid prototyping, EnvisionTEC committed 2014 to new materials and machines for custom solutions.
The Perfactory® Desktop XL is the new chairside machine that brings power to your workstation. Featuring a larger build envelope than the Micro, the Desktop XL answers the call for a flexible 3D printing solution for small businesses.
After much anticipation, EnvisionTEC formally released the Xtreme® 3SP®. The sister 3D printer to the Xede® 3SP®, the Xtreme features large-frame capabilities with a build size of 10” x 15” x 13”. Debuting at EuroMold 2014, the Xtreme brings larger than life 3SP precision to manufacturing.
To round out 3SP solutions, EnvisionTEC released an array of new materials for MCAD applications. These include E-Glass 3SP featuring glass-like clarity for verification and design purposes, along with ABS-like plastics for 3SP, Perfactory and Micro systems, including ABS Flex and ABS Tough. Finally, Superflex offers a durable yet flexible polypropylene-like properties upon curing. These new series offer a gamut of flexural strength and durability to back the end use of these parts in a variety of functions.
» Biomedical
Finally, EnvisionTEC is proud to recap 2014 as a great year for biomedical advancements made with EnvisionTEC systems. The 3D-Bioplotter® won the DeviceMed Award at the 2014 COMPAMED Trade Fair, and has featured in several research projects. EnvisionTEC released the Bioplotter Developer series with 5 depositories for advanced operations, and went on the showcase the system around the world, in the USA, Asia and in Europe.
Northwestern’s SHAH Lab was very active this year with their Bioplotter research. At RAPID 2014, Dr. Ramille Shah’s team presented work with developing scaffolds that become tissue and integrate into the body. This year SHAH Lab SHAH Lab also announced
3D-ink materials, which work within scaffolds in order to mimick and repair parts of the human body. Dr. Rocky Tuan at the University of Pittsburgh has broken through with 3D printed cartilage using light processing of the DLP technology, while researchers at Columbia University have created a 3D printed knee meniscus to see implantation in 2015.
We had a great year in 2014, thanks to all our amazing clients, partners, and staff! Here’s to another good one — come build the future with us.