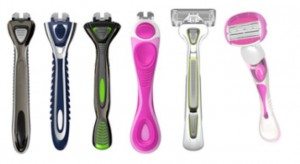
EnvisionTEC 3D Printers Reduce NPD Costs at Dorco
One of the first – and still most successful – applications of 3D printing is within the New Product Development (NPD) process. This case study illustrates how Korean company, Dorco, has saved time and money by employing an EnvisionTEC ULTRA® 3D printer for design verification.
Dorco is a company in the Korean razor, razor blade, kitchen knives and stationery cutters market and has been manufacturing and exporting the highest quality products in its sector for 55 years to a global market. The company has had to adapt and improve its product development processes over the last six decades to maintain its market position and continue to develop superior product ranges.
One of the most recent adaptations, which has seen tremendous results, was to embrace 3D printing within the new product development process.The company’s 3D printer of choice was an EnvisionTEC Ultra, the scale and accuracy of which has dramatically improved the design verification process at DORCO and brought significant cost reductions due to less prototype tooling. Before the implementation of the 3D printer, DORCO’s traditional process involved designing a product in 3D CAD, in this case a razor cartridge and handle, then manufacturing a Quick Delivery Mold (QDM).
Beyond the timing, however, the cost for this repetitive QDM process for these two products alone would be in the region of 2,200,000 SK Won (£1315) for the Cartridge and 5,000,000 SK Won (£2988) for the handle.After molding the designs would need modification and subsequently another QDM tool would be manufactured and the parts analysed once again.This process, of necessity,would be be repeated several times — sometime as many as ten molds would be created before the design was passed and a production tool manufactured! This process would typically take between six and eight weeks, meaning that design agreement and final production would be held up and time-to-market delayed.
In 2013, DORCO purchased the EnvisionTEC Ultra and immediately started using it to produce visualization models and functional models with the EnvisionTEC R5 material. By using the models directly from the machine for design review and assembly trial, DORCO has eliminated the need for the QDM tools entirely as the parts are ready for use from the Ultra within hours. Instead of taking the previous 6-8 weeks to verify a design for production tooling it now takes approximately 10 days!
It now costs 800 SK Won (£0.48) for the cartridge and 8,000 SK Won (£4.78) for the handle — a saving of over 7 million SK Won (or £4180) per design! Meaning that the 3D printer quickly paid for itself.
Furthermore, because of the savings in time, designers at DORCO have more time to experiment with new designs for electric razors.