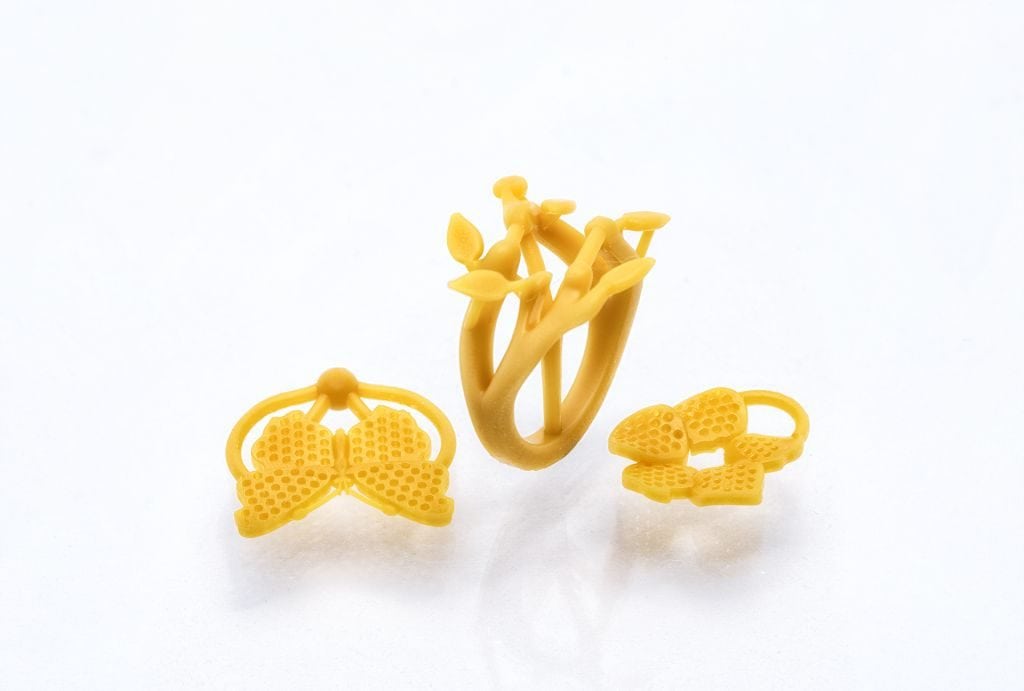
Bosmans Jewelry 3D Printing with a Perfactory® Micro
In 1983 Andre Bosmans, based in Belgium, founded the independent jewelry company, Bosmans, specializing in bespoke handmade fine jewelry design and production with a focus on creativity and innovation. Later on Andre’s wife, a goldsmith, joined him in this venture enabling the company to design and manufacture everything in house; but through necessity, prototyping processes were outsourced.
For many of Bosmans’ clients, confidentiality is of paramount importance, and balancing this with a fast, accurate and cost-effective product development process proved challenging. As a designer of fine jewelry, Andre has been working with 3D CAD for some time and is experienced with 3D software such as Matrix, Modo 601,T-Splines and ZBrush.
Showing his clients designs and renderings using this software was also proving something of a challenge and many were starting to demand 3D printed models for fast turn around approval of designs and high quality 3D printed masters were also required for casting of the final products. To meet this demand, all of the 3D printing work was outsourced to partner companies, raising confidentiality issues.
3D printed ringsLast year Bosmans made the decision to bring this service in house to ensure that all clients’ designs remained wholly within the company’s control, and started looking for a fast, highly accurate and cost-effective 3D printing solution that would meet the company’s needs.
Bosmans has benefitted in all of these areas, with noticeably faster turnaround times for clients, significant cost savings over outsourcing to 3DP service bureaus and producing higher quality results. The Perfactory® Micro 3D printer has also had the desired effect of eliminating all confidentiality issues and, as a bonus, Bosmans now has much greater control over the entire product development process from first concept through to final production with true flexibility to operate in the best interests of the company.
“We save 3–5 days per model in production time and more than 50% of outsourced master pattern costs. And, we have gained so much new business, due the fact we have full control of the design and 3D Printing.”
– Andre Bosman
Bosmans is now continuing to use the Perfactory® Micro 3D printer to support the creative design to manufacture process and introducing real innovations in jewelry to this market as a result.
Furthermore, Andre Bosmans is so impressed with the benefits that the company is realizing, that: “We are considering buying a larger machine from EnvisionTEC within the next 6-8 months.”
Some specific examples of where Bosmans is reaping the rewards of implementing 3D printing in house include:
- Designers are able to try out their ideas free from the cost and time constraints imposed by traditional outsourced prototyping.
- Sample Production: Using the Perfactory® Micro, samples can be 3D printed in a matter of hours and then electroplated to give the precise look and feel of the finished product.
- Design Verification: 3D printed models can be checked against the 3D CAD model for design intent and measured for accuracy and sizing.
- Master Patterns: Parts are 3D printed in wax filled resin and cast following a normal casting route. A wide variety of materials can be processed, including Platinum.
- Patterns for Rubber Molds: The high temperature resin, HTM140, can be used for hot rubber mold manufacturing.
- Production: Full production of unique pieces are manufactured with the Perfactory® Micro at the center of production — Bosmans is producing 6–9 pieces every day.